Spot welding robot is widely used to weld thin plate materials, and the spot welding operation accounts for most of the car body assembly project in automobile factory. The welding gun held by the robot arm includes electrode, cable, gas pipe, cooling water pipe and welding transformer. The welding gun is relatively heavy, which requires the arm to have strong load capacity. Now the DC post AC servo motor drive mode has met the requirements, its repeated positioning accuracy can reach + 0.30 ~ 1 mm soil, the quality assurance is consistent, so it still occupies a large proportion in industrial robots.
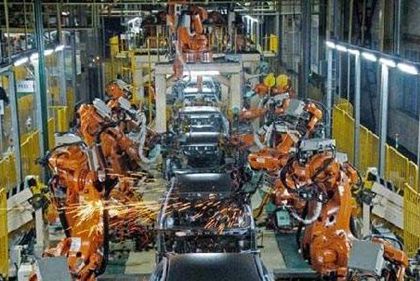
The attached figure shows the schematic diagram of the spot welding robot. The moving axis of the robot is a six axis joint type. The motor M1 drives the rotation of the rotary table to realize the movement of the first axis; the motor M2 drives the swing of the boom 2 to realize the movement of the second axis; the motor m3 drives the swing of the boom 12 to realize the movement of the third axis; the motor groups M4, M5 and M6 drive the wrist through the real or hollow shafts Do. In order to keep the structure as rigid as possible, avoid large inertia torque, and keep high speed until it is transmitted to the working end, the first axis uses cycloidal pin wheel reducer, the second and third axes use ball screw, and the wrist parts use harmonic gear alkali speed reducer. In addition, in order to counteract the influence of inertia force, a balancing cylinder is arranged on the second and third shafts.
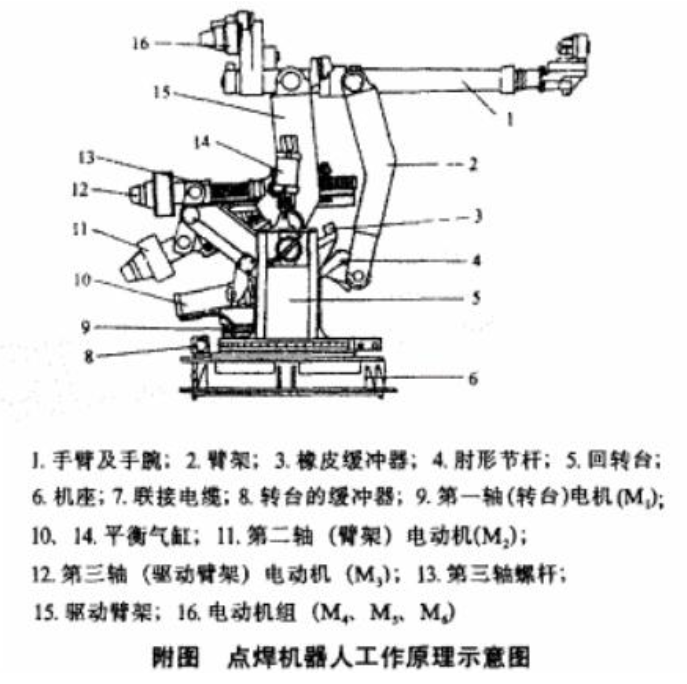